プラスチック材料に色を付けるために、何をしているのか?
皆さんの身近にある様々なプラスチック製品。
黒や白の他にも色鮮やかな製品が世の中にはたくさんあります。
しかし、多くのプラスチック製品の原料となるポリプロピレンやポリエチレンをはじめ、多くの樹脂はもともと透明や乳白色をしています。
では色鮮やかなプラスチックはどんな方法で色がつけられているかご存知でしょうか?
今記事では弊社で主に取り扱っております射出成形原料の着色方法について解説いたします。
プラスチックの外部着色、内部着色
プラスチックに色をつけるには大きく分けて外部着色と内部着色という2つの方法があり
着色方法としてそれぞれにおいて全く違い、一長一短あります。
外部着色とは
色の入っていないナチュラル色で成形しその後、表面に印刷や塗装などで色を付ける方法です。
主に塗装、メッキ、印刷の3種類に分けられます。基本的に木材などと同様にウレタン系やアクリル系の塗装材を塗ることができます。
長所
・内部着色では表現できないような色付けが可能
・製品1個から着色できる
短所
・樹脂によっては密着性が良くないため下処理が必要
・内部着色に比べコストがかかる
内部着色とは
樹脂全体に色を練り込んでいる状態を指し、外側の色と断面は同じ色になっています。
着色材を樹脂原料と一緒に練り込むため、内部まで均一に着色することができます。
長所
・着色材が均一に混ざっているため発色が良い
・塗装に比べ、大量生産に適している
・2次加工によるコストが抑えられる
短所
・コンパウンド品では原料在庫を保管するスペースが必要
機能性着色材
樹脂業界における着色剤とは色を付与するだけではありません。
「機能性着色剤」と呼び、色粉そのものが機能性を持つもので、例えば自動車のバンパーやコンテナなどは、カーボンブラック(加工ナシ)を着色剤として用いることで、耐候性を向上させています。
その他にも特性を付与する添加剤を着色材とともに混ぜ合わせ、再生材料へ機能性を付与させることが可能です。
中定樹脂の樹脂着色
ここからは主に中定樹脂が持つ ドライカラー、マスターバッチ、カラーコンパウンド 3種類の着色技術を紹介いたします。
ドライカラー
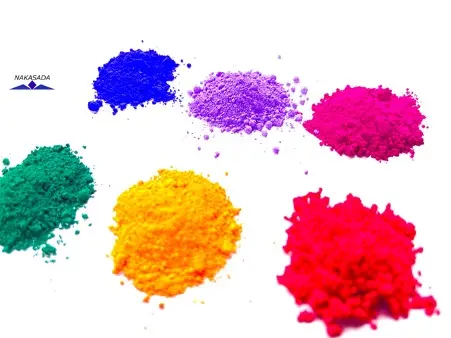
ドライカラーとは最終製品のカラーに合わせた調色レシピ通りの配合にて、顔料や染料(着色材)に微粉末の分散剤を混ぜ合わせて製造します。
ドライカラーにおいて大事なことは、着色材をしっかり分散させることです。
顔料粒子が集まり凝集しないように、金属石鹸や脂肪酸系滑剤など、各樹脂に合わせた分散剤を使用し素材の粒子同士の摩擦を限りなく軽減させることにより、表面の発色は安定します。
着色方法の中でコンパウンドやマスターバッチに比べ安価な一方で、タンブラーや成形機、乾燥機など様々なものに付着したり、工場内を飛散することで他の品物にも影響が出る可能性があり、材料切り替え時に時間を要することがあるため、人的コストがかかります。
使い方としては着色材を樹脂原料とともに均一タンブラーに投入しブレンドオイルを用いて、樹脂の表面に付着させたのち、成形機に投入します。
ドライブレンド加工
混合機設備や人手が確保できないユーザー向けに中定樹脂でタンブラー加工を承ります。
混合タンブラー機を使い、原料のベースになるペレットや粉砕材などに、染料や顔料などの着色材やマスターバッチ、各種添加剤などを均一に混ぜ合わせて着色します。
この着色方法は粉末が飛び散り工場内汚染の恐れや、色のムラが出てくるケースもある反面、加工賃を安く抑えたい場合や、納期を急がれているお客様には最適です。
マスターバッチ
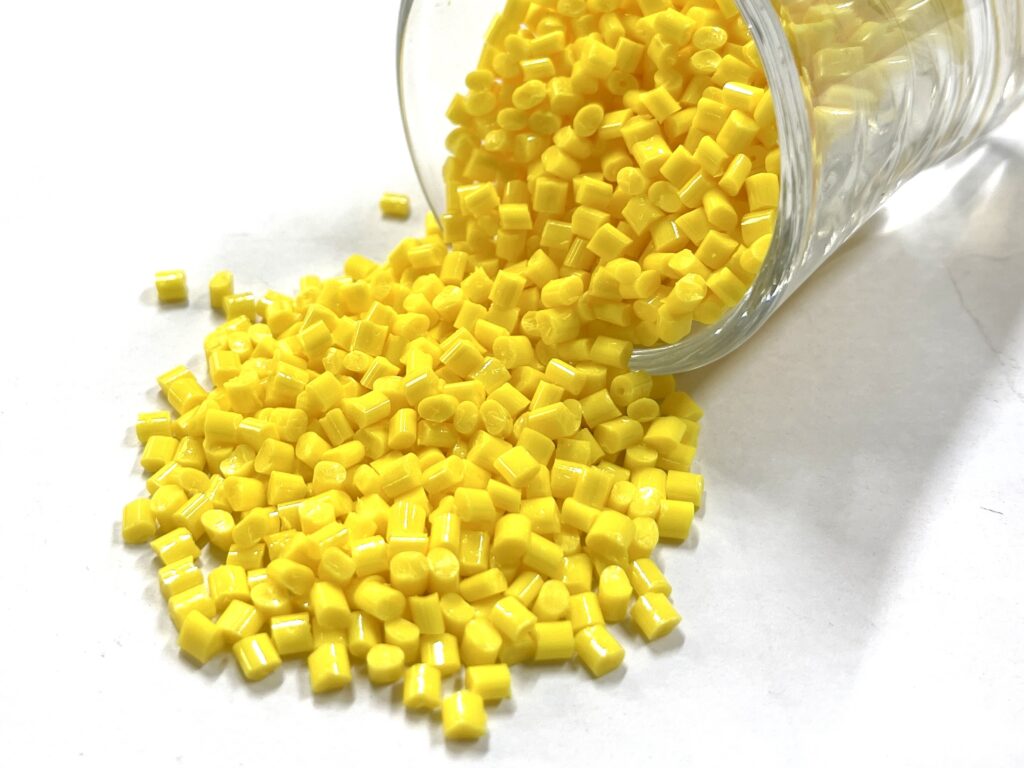
マスターバッチとは少量のベース樹脂に対して一般的には2倍〜50倍の着色材を、ブラックなどでは100倍のカーボン顔料をコンパウンドしたペレットのです。(よくカルピスの現役に例えられています。)いわば超高濃度な着色ペレットということです。
その他にも各種、添加剤を練り込んだマスターバッチも数多く存在します。
添加剤の種類によりカラーコンパウンドしてしまうと色分け等が生じ、製品外観に影響を及ぼす可能性があるため、成形時に成形機にてマスターバッチを混ぜ合わせなければならない場合もあります。
使い方としては、製品カラーの規格に応じた量のマスターバッチをナチュラルペレットで希釈し成形機に投入します。配合機を使う場合や、タンブラーで均一に混ぜ合わせる方法があります。
注意点として、マスターバッチ自体の着色材分散性はもちろん大事ですが、その上で成形機内にて両者を練り合わせる必要があるので、L/Dの低い成形機を使用する場合の混錬不足や比重の違いにより、色むらや色筋が出てくる場合があります。
ある程度は出来るだけ成形条件を整えながら成形します。
デザイン的な表面色の要求が高い製品の場合は次のカラーコンパウンドが多く使われています。
ドライカラーに比べ価格は上がりますが、空間汚染等や機械設備を考えると作業性は遥かに上がります。さらに着色コンパウンドに比べると在庫を抱えなくて良く置き場を取らないメリットがあります。
カラーコンパウンド
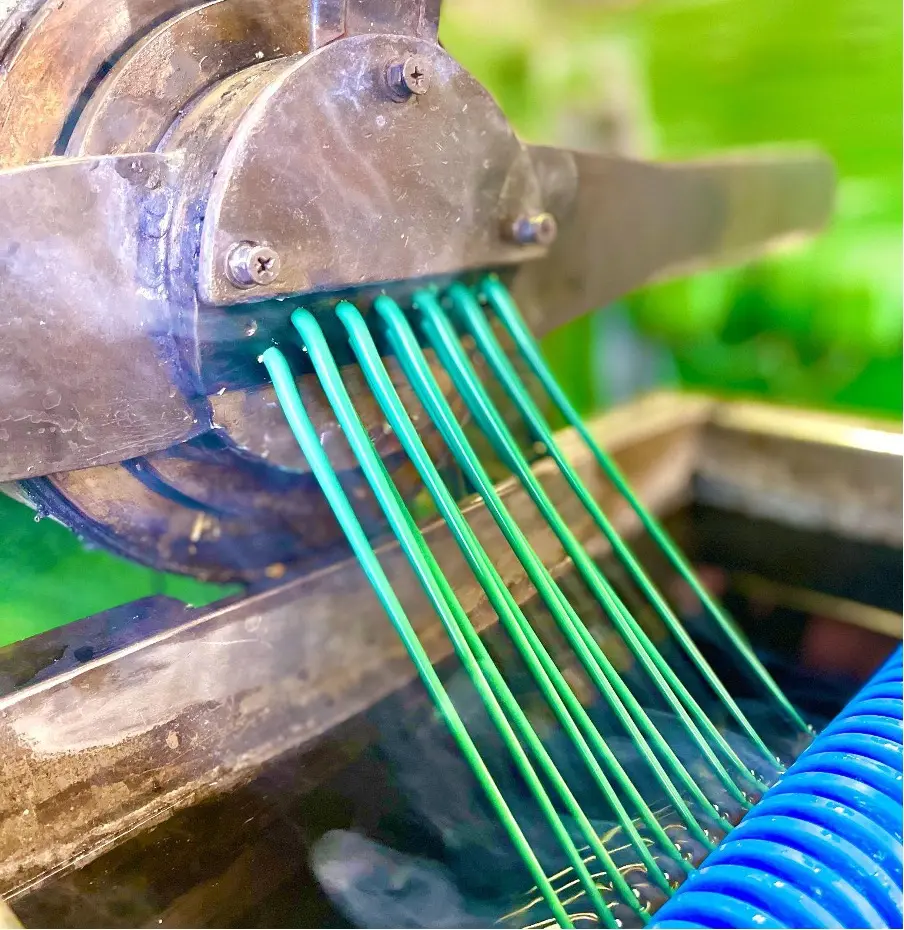
着色コンパウンドとは成形樹脂材料に対し製品のカラーにて1倍の濃度で着色材を練り込む方法です。
着色ペレット(着ペレ)などと呼ばれます。
マスターバッチ同様、抗菌剤や耐候剤など各種添加剤を添加し機能性を付与させる事もできます。
さらに強度を付与するグラスファイバー(ガラス繊維)や寸法安定性や製品の比重などを目的とするタルクや炭酸カルシウムなどのフィラーコンパウンドも同時に可能です。
使い方はすでに最終製品の仕様、カラーになっていますのでナチュラルで希釈せずにそのまま使用できるため、色むらやフィラーなど分散性の心配がなく、高品質の製品が仕上がります。
ですが他の着色方法と比べ高価なことに加え、使用するには在庫を保管するスペースの確保が必要となります。
このように長所と短所がハッキリとしているため、それぞれに特徴はありますが、試作も含めて最終製品や製造条件により適切な方法を選定することができます。
弊社ではバージン材の受託カラーコンパウンドから再生材のカラーコンパウンド、そして各種再生ブラックペレットの販売を行なっております。
再生材の使用では、なるだけ安定した物性の材料を提供出来るよう、排出事業者様はもちろん再生材料を取り扱う多くの業者様とお取引をして頂いております。
また、排出事業者様から頂くお仕事では、端材や成形不良などを粉砕し、着色材等は何も加えずにリペレット加工しお返しする場合や、他製品向けに着色済みのプレコンシューマー材を再び違う色にカラーコンパウンドし、再商品化の材料確保のお手伝いもさせていただいております。
まとめ
ドライカラー
長所
- 他の着色方法に比べて安価である
- 最も短納期や小ロット向け
- 場所をとらない
短所
- 飛散や付着による作業性低下
- やや軽量が難しいことも
- 色むらなどの可能性
マスターバッチ
長所
- カラーコンパウンドにくらべてトータルで安価
- 成形材料の物性低下の比率が低い
- 飛散や機材汚染がない
短所
- 混合タンブラー機やサイドフィーダー等の設備が必要
- カラーコンパウンドに比べ色むらの可能性
- ナチュラルペレットとの比重の違いから投入後から経過での色ブレの可能性
カラーコンパウンド
長所
- 色の安定性に優れる
- 最終製品と同じ色味なため、余計な準備作業がいらない
短所
- すべてを均一に着色するため他の着色方法と比べ高価
- 在庫スペースの確保が必要