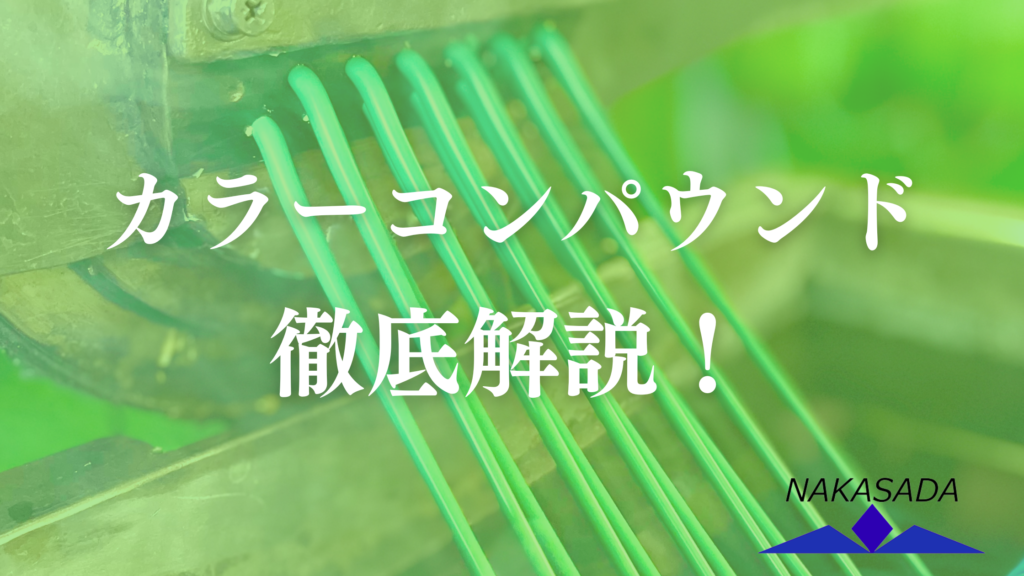
こんにちは。いつも大変お世話になっております。
本日は、当社の主軸となるカラーコンパウンドおよび加工業務について、その内容や設備についてご紹介いたします。
カラーコンパウンドとは、プラスチック成形に使用される原料に着色材を練り込み、最終製品のカラーに合わせた均一なカラーペレットを製造する手法です。
樹脂の着色方法にはさまざまな呼び方があり、業種や会社によって異なります。
カラーコンパウンドの他にも、バージン着色品、着色コンパウンド品、着色ルーダー加工、着色ペレットなどと呼ばれることもあります。
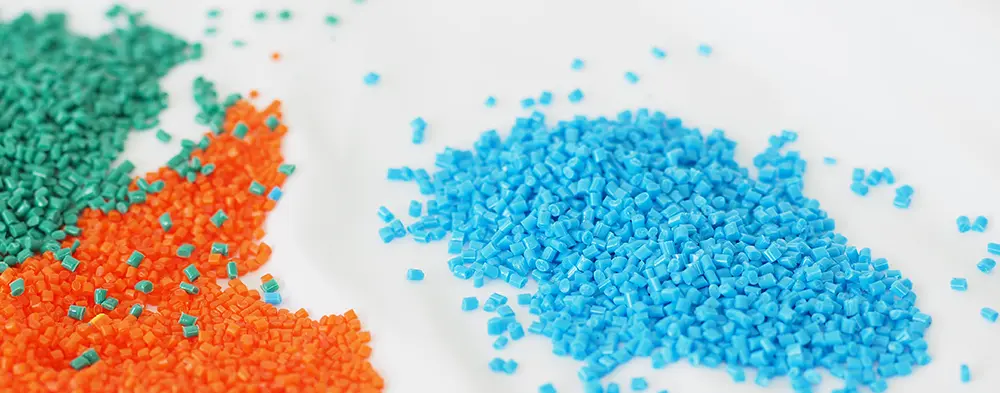
当社のカラーリング事業では大きく分けてバージン材(メーカー新材)へのカラーリング、再生材へのカラーリング、この2つに分かれており、その中でもユーザー様から原材料を支給していただき、着色する場合と、当社の原料在庫や入手ルートを駆使し、材料調達から着色まで一貫して行う場合があります。
カラーコンパウンド品のメリットとして、マスターバッチやドライカラー着色と比べ、色むらや機械汚染が無いため作業性が良く、原料のブレンドなど成形前作業を省けます。それに原料全体に着色材を均一に練り込むため発色においては1番良い方法と言えるでしょう。
この辺りはこちら記事で解説しておりますので是非ご参考にご覧ください。→中定樹脂のカラーリング技術
それではまず、樹脂のコンパウンドに使用する押出機という機械の説明から、大まかに着色ペレットを製造する流れとその際に必要となるそれぞれの機械に必要なことや注意する点などを紹介していきたいと思います。
カラーコンパウンドに使用する押出機とは
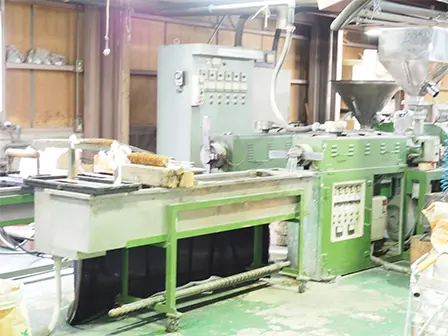
樹脂をカラーコンパウンドする方法として、弊社ではベント式のエクストルーダー機というものを使用いたします。
ベント式というのは、シリンダーの途中に通気口が設けられております。
そこから樹脂に含まれるガスや水蒸気などが排出できる仕組みになっており、そこに真空ポンプという装置を繋ぎシリンダー内を真空状態にする事でコンパウンド性能を向上させています。
真空ポンプ装置自体はバージン材のカラーリングには無くても困らない場合もありますが、粉砕材をはじめとする再生材を扱う場合はこのベント→真空ポンプがなければ高品質な再生原料は作れません。
ルーダー機は押出機ともいわれ、加熱シリンダーの中にスクリューが入っており回転により溶融させた樹脂を先端方向に押し出していく方法です。樹脂を前に押し出すスクリューには単軸と2軸に分けられ、それぞれに特性があります。
・2軸スクリューとはシリンダー内で2本のスクリューが同方向または異方向に回転し樹脂を溶融、送り出します。
もともと持つせん断力に加え、エレメントをエレメントをエリアごとに変更できることから高分散が求められる高濃度マスターバッチや、複合樹脂のコンパウンド、さらに流動性が低く劣化しやすいポリマー加工に適しています。
・単軸スクリューとはシリンダー内で一本のスクリューが樹脂を溶融、混錬します。
押し出す力に優れているため、パイプなどを作る押出成形においてはほぼ単軸が使用されています。
汎用的な着色コンパウンドやリペレット加工に適しており、せん断力が2軸と比べて低いため樹脂の熱劣化を抑えることが可能です。
いくつかの要因から稀に発生する混錬不足にはスクリュー形状に合わせた押出速度や温度条件の設定で解消できることが多いです。
どちらも一長一短あり、それぞれのスクリュー設計により様々な特性を持たせることができます。
グラスファイバーやカーボンファイバーなど、様々なフィラーを扱う場合、スクリューやシリンダーに特殊な加工が必要になります。一般的な設備で生産すると、シリンダー内の摩耗性によるスリ減りや、その他機械設備への悪影響から、カラーコンパウンド品に悪影響を及ぼします。
ここからは着色コンパウンドの流れや、それに伴う注意点など簡単に説明していきます。
着色コンパウンドの作業工程
①着色材料の仕込み
調色データに基づき、これから着色する樹脂の数量に適した顔料や染料、分散材を混ぜ合わせ着色材を作成します。
混合タンブラー機を使用し、ベースとなる樹脂と着色材を均一に混ぜ合わせます。
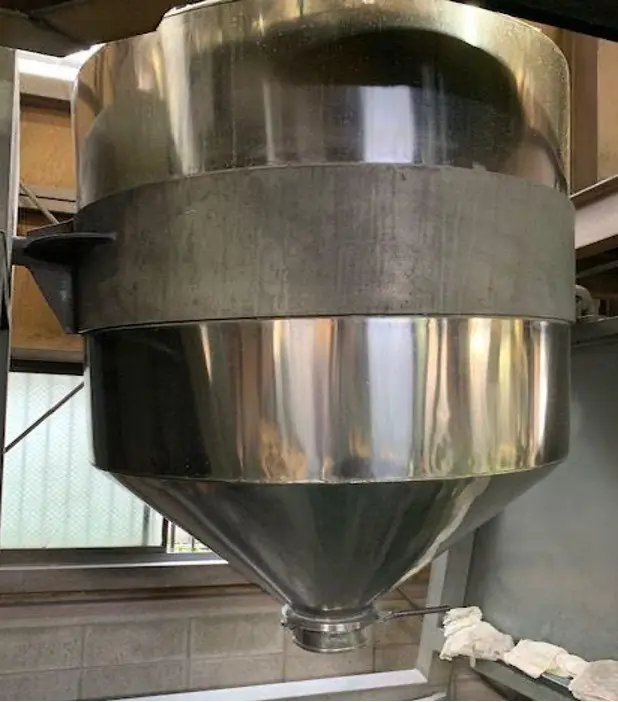
ここで、着色剤がタンブラー内で飛散してしまうと色の違いを起こしてしまいます。
ただでさえ押し出し条件によって着色材の反応も変わり、思うような色が出てこない時もあるので、仕込み時の色ズレは極力抑えなければなりません。
着色材と樹脂のバランスに適した量のブレンドオイルを使用しベース樹脂と着色材を吸着させます。
②押し出し工程
エクストルーダーのシリンダー内も一案件ごとに分解して清掃は出来ませんので、切り替え時には確実にパージしていきます。
それでもコンタミというのはシリンダー内に残留してしまうのでスクリーンメッシュを使い分け、コンタミ除去に努めなければなりません。
ホッパーから投入された樹脂が溶融しながらスクリュー回転により前に押し出されてきます。基本的にホッパー下は加熱しないように、水通しをするなどして対策します。
送り出された先には金型の役割を果たすダイスと呼ばれるものを通し、ストランド(樹脂がパスタ状になって出てきたもの)が吐出されます。
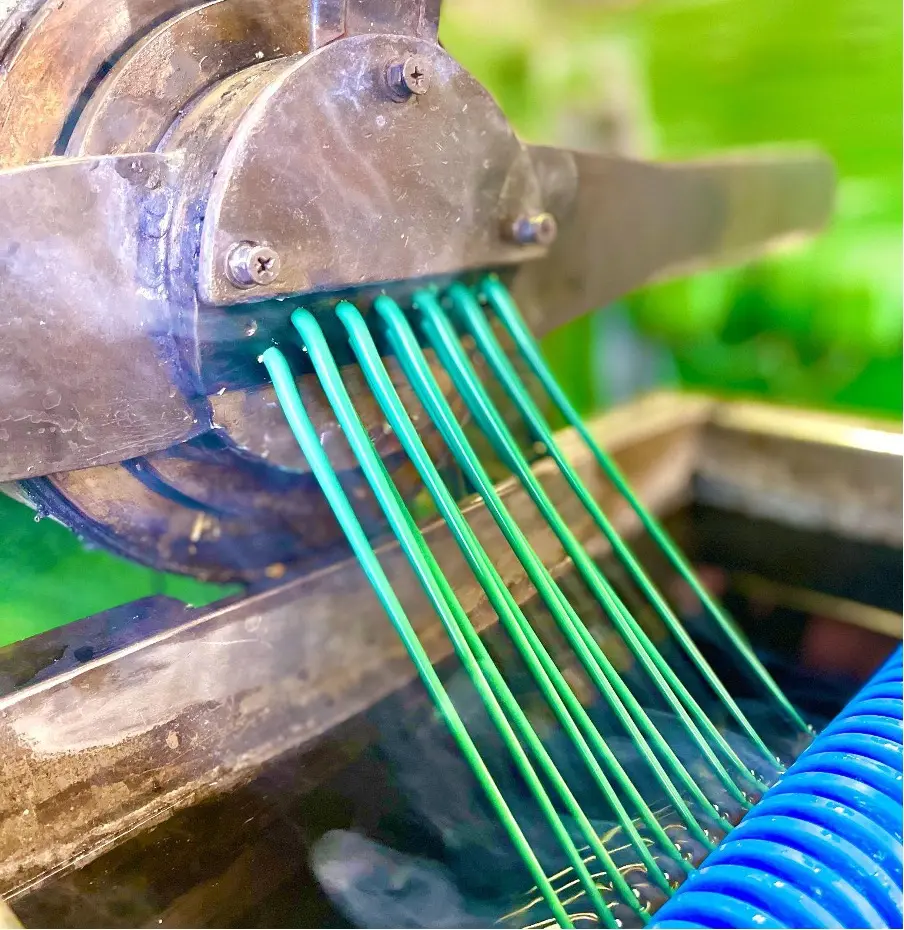
大前提として、樹脂は熱を加える度に劣化します。
コンパウンドするには素材そのものの物性値をできるだけ低下させないことが絶対条件となります。長年のノウハウを生かし、樹脂にとって最適な条件を作り出します。
それに加工時は新材、再生材に関わらずストランドが出てくるダイスの部分はコンパウンドする樹脂によって、特性が様々なため形状や大きさを変えなければ安定して押し出すことが出来ません。(ストランドが切れてしまったり、ひっついてしまう)
そのため、ダイスは形状や穴数の違うものを数種類、使い分けなければなりません。
そしてもう一つ大事なのが異物の混入を防ぐことです。
そのため、生産前にはエクストルーダーのシリンダー内を確実にパージしていきます。パージ材や各種ナチュラル材を使い色を抜き、樹脂を切り替えます。1カラーごとに分解して清掃は出来ませんので、前回分解清掃時からの履歴や現状のパージ具合を確認し、しっかりとした下準備をした上で不良を出さないようにします。
それでもコンタミの原因となるようなものはシリンダー内に必ず残留していますので、スクリーンメッシュを使い分け、コンタミ除去に努めなければなりません。
③冷却
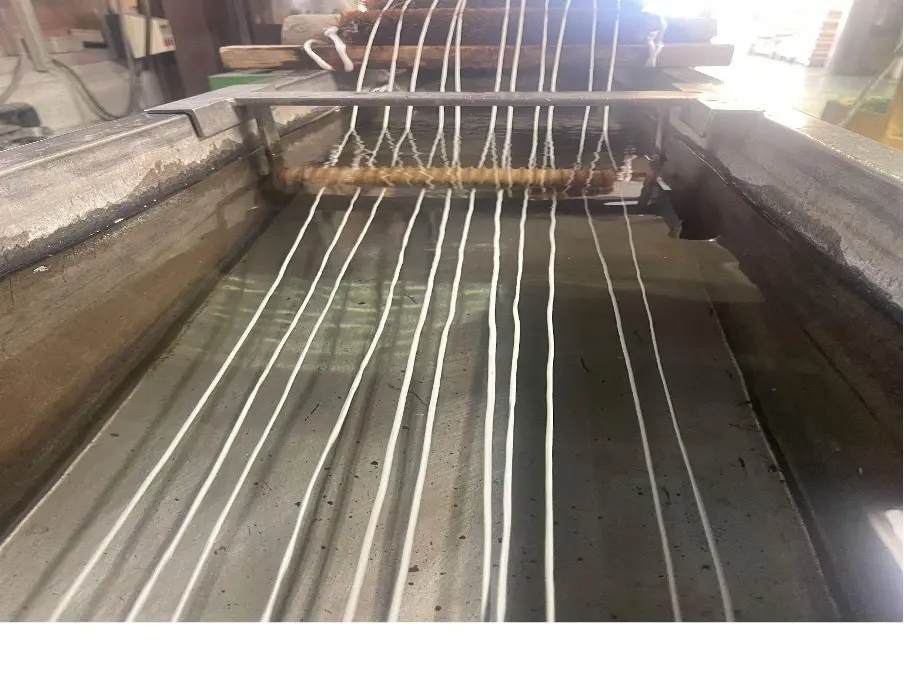
ダイスから吐出されたストランドを水槽を通して冷却し、固化させます。ここで、水槽内の温度ですが、高すぎても低すぎてもいけません。
ストランドが断続的に通ることで水温は上昇し続けます。
流入する水の量を調節し、樹脂ごとにストランドの挙動を確認しながら温度調節しなければ安定した量産体制に入れません。
④カッティング
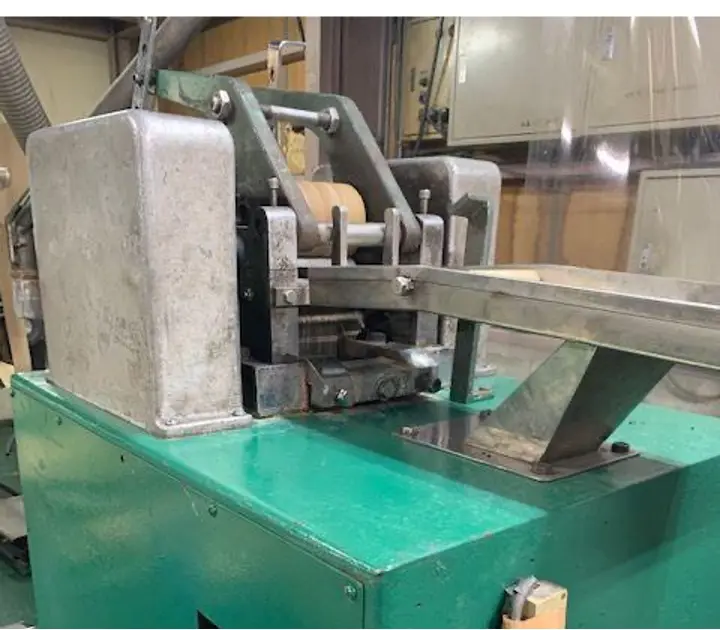
水切り装置などで余分な水分を飛ばした後、ペレット状にカットする機械に巻き込み、断続的にカッティングすることで着色ペレットが出来上がります。
この機械はペレタイザーといい、ホットカットシステムとの呼び分けから、ストランドカッターとも呼ばれています。
カッティングの種類についてはまた別の記事で書きます。
ペレット状にカットされた樹脂は選別機というもので、成形トラブルを起こすレベルの規格外ペレットを弾き、付属のホースにてキャッチャータンクへ送り込むことで、着色材料の出来上がりです。
⑤色判定
仕上がった着色ペレットで射出成形機を使用し、プレート状のものを成形します。
成形したプレートと依頼された色に差がないか測色、色差計を用いて確認し、合格であれば量産となりますが、ここで補色が必要な場合、調色作業に入ります。
終了後は生産条件や生産プレート、着色データの保管に注意を払い、安定したカラーリングを継続できるよう努めます。
カラーコンパウンドを行う上で、バージン材に関してはある程度、グレードごとに決められた条件や樹脂ごとの加工ノウハウが揃っていますが、樹脂は繊細な部分もあります。
保管状況や、製造環境に合わせた最適の条件で品物を完成させなければなりません。
さらに要所ごとに細かな注意点やトラブル機械があり、弊社ではそれらに対応、改善しながら日々、奮闘しています。
カラーコンパウンドの製造過程まとめ
①仕込み
ベースとなる樹脂と着色材を均一に混ぜ合わせる
仕様により、各種添加剤を共に投入します。
※色のブレに繋がるので飛散しないよう、ブレンドオイルを適量入れ、混ぜる。
②押出し
①での材料をエクストルーダーのホッパーから投入する。
※生産前にしっかりシリンダー内を清掃し、生産する樹脂に切り替えます。
低音パージや高温パージを行い、状況によりスクリューを抜いて分解清掃します。
③冷却
②で出てきたストランドを水槽内で冷却。
※水温、水に浸ける長さ等に注意する。
④カッティング
※冷えて固まったストランドをペレタイザーに巻き込み回転刃と固定刃にてペレット状にカットします。
規格外のペレットが混入しないよう気をつける。
⑤色調判定
※量産体制に入る前にコンパウンドしたペレットを射出成形機にてプレート状に成形します。
規定通りの色との差がないか測色計を用いてチェックします。
その後、量産に入ります。
以上がおおまかな着色コンパウンドの流れとなります。
カラーコンパウンドによる着色ペレットの製造についてなんとなく理解できたでしょうか。
これからは実際に私が経験した加工トラブルや再生材のコンパウンドについても記事にしていきますので今後ともよろしくお願いいたします。