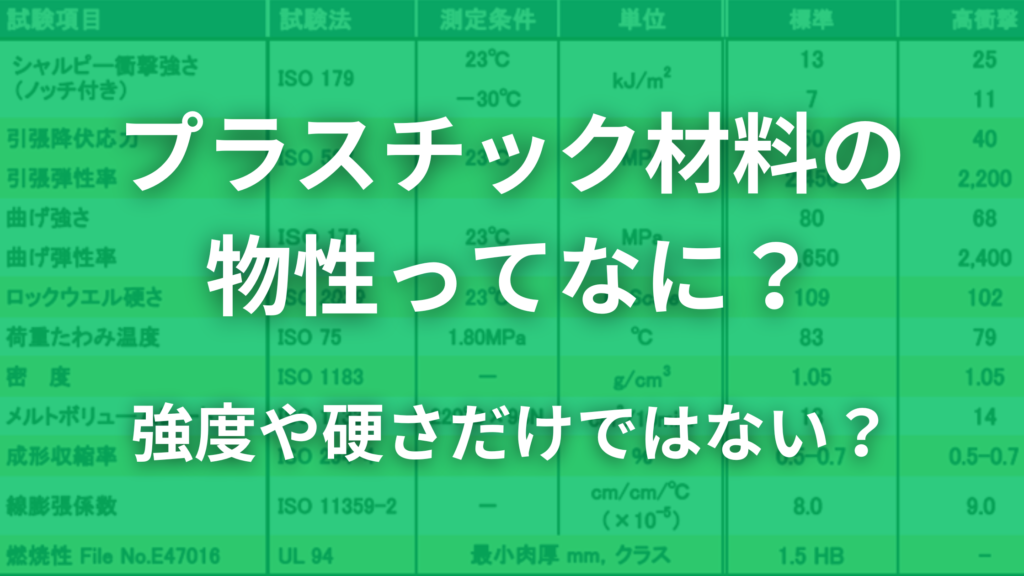
物性とは、材料や物質が持つ固有の性質や特性を指し、これらを具体的な数値データとして表現したものは、材料選定における極めて重要な指標となります。
鉄、アルミニウム、樹脂など、多種多様な材料が存在し、それぞれ異なる物性を備えています。この物性データは、製品の設計や製造において、材料の特性を理解しやすくするための貴重な情報源となっています。
近年、環境への意識が高まる中で、再生原料の使用が増加しています。これは、従来のコスト中心のアプローチから、持続可能性を考慮した環境への配慮が拡大していることを反映しています。今後、再生原料は雑貨だけでなく、家電、家具、自動車部品など、機械的特性が要求される製品にも広く採用されることは間違いありません。この際、再生原料も特定の物性を備えている必要があり、その性質を理解することがますます重要になることが予想されます。
この記事では、プラスチック材料に関する物性項目と、それらを数値化するための試験方法について詳しく解説していきます。
材料選定から製品設計において、物性データは不可欠な要素となり、持続可能な未来への貢献にも繋がってきます。
機械的性質
機械的性質とは材料の力学的な特性のことを指します。
プラスチック製品の設計においてこの機械的な強度や特性が特に重視されることが多く、プラスチックに荷重を加えると材料は変形し、最後は破壊しますが、この荷重を加えたときに起こる変形具合や、原料の強さなどの機械的変化に関連する性質を一般的に機械的性質と呼びます。
①力が加わった時、破壊するまでにどれだけ耐えれるかは「強度」
試験片が破断する時の荷重の大きさを表します。曲げ、引っ張り、圧縮強度などが代表的です。
②力が加わった時、変形のしにくさを表すのは「剛性」
代表的なのは曲げ弾性や引っ張り弾性です。柔らかいものは弾性が低く、硬いものは高い。
③表面の硬さを表し、傷つきにくさや変形しにくさを表すのは「硬度」
この辺りは少し小難しい内容となりますので、大体のイメージがつけばとりあえずは大丈夫です。
引っ張り強さ
プラスチック試験片に引っ張り荷重を加えて、それが破断するときの最大荷重を試験片のもとの断面積で除した(割り算した)値のことでMPaで表される。引っ張り強さは試験条件の相違によって測定値が変化します。測定する際に、引っ張り速度やその温度を変えることによって著しく引っ張り強さや伸びが変化します。実際には大きな機械に試験片の片側を固定しもう一方を引っ張っていくような試験です。
引張り降伏点強さ
プラスチック試験片に一定速度で引っ張り荷重を加えると、荷重と伸びの関係から降伏点を境にして塑性流動による変形を起こし破談に至る。この際の降伏点における荷重を試験片のもとの断面積で除した値を引っ張り降伏点強さとする。
プラスチックの性質や測定条件によっては破断するときの荷重から求めた引っ張り強さよりも大きい場合がある。(JIS K 7161−1では引張降伏応力と呼びます)こちらも前述の引っ張り強さと同様の試験方法となります。
破断点伸度
プラスチック試験片に一定速度で引張り荷重を加え破断点における試験片の標点間の伸びを百分率で表す。
(JIS K7161−1)では引張り降伏応力に対応する歪みには引っ張り降伏ひずみ、降伏を伴わずに破壊する場合は引張り破壊ひずみ、降伏後に破壊する場合は引張り破壊呼びひずみを用いる。
曲げ強さ
試験片を2支点上で水平に置き、上部中央から加圧クサビで曲げ荷重を加え、試験片が破断する際の最大荷重をMPaで表します。
一般に試験片の形状、寸法、加圧クサビの曲率半径、支点間距離および荷重の速度などで測定値が左右されるので試験方法の規定に準拠することが必要です。
曲げ弾性率
試験片を2支点上に水平に置き、試験片の上部中央から加圧クサビで荷重を加えていくと試験片にひずみが発生します。
この際の荷重とひずみの関係が弾性限界内と仮定して、この比を曲げ弾性率(MPaまたはGPaとしています)
デュロメーター硬さ
こちらはプラスチックの中でもエラストマー樹脂に対して使われることが多いです。
押し針を試験片表面に押し付けた時の押し込み深さを基に硬さを測ります。デュロメーターにはタイプA、タイプD、タイプEとあり
それぞれ硬さによって使い分けられます。
A:タイプDデュロメータで硬さが20未満の値を示す場合に使う。一番よく使用されます。
D:タイプAデュロメータで硬さが90を超える値を示す場合に使う。硬いエラストマー等でよく使います。
E:タイプAデュロメータで硬さが20未満の値を示す場合に使う。これは柔らかいゴムでしか使いません。
エラストマー樹脂における成形だけでなく、原料コンパウンド時にも必要となる硬さです。
ロックウェル表面硬度
試験片に鋼玉を押し込み、その際に試験片にできた凹みの深さから、表面硬度の数値を求めます。
ロックウェル表面硬度は試験片に加える荷重と鋼玉の径との組み合わせで表します。
プラスチックにはR、L、Mの3種のスケールが使用されています。
シャルピー衝撃強さ
ノッチを有する試験片を水平に置き、試験片のノッチ部分の背面に向けて、所定位置からハンマーを振り下ろして一撃で試験片を破壊した時のハンマーの振り上げ角からシャルピー衝撃強さ(kJ/㎡)を求めます。
衝撃荷重に対する抵抗を求める試験の一方法ですが比較的、測定値のばらつきが大きいとされています。
JIS K6911などではこのシャルピー衝撃強さ試験方が採用されています。
アイゾット衝撃強さ
一端を固定し、切り込み部をハンマーの方向に向けた試験片に所定位置からハンマーを振り下ろし、1回の衝撃で試験片を破壊した時のハンマーの振り上げ角からアイゾット衝撃強さ(kJ/㎡)を求めます。
シャルピー衝撃強さと同様に衝撃荷重に対する抵抗を求める試験の一方法ですが、こちらの場合も比較的測定のばらつきが多いとされます。
基礎的性質
密度
密度とは標準試験室温度における物質の単位体積あたりの質量のことを言います。
製品の軽量化など目的に対して重要な要素となっており、単位はg /㎤。
同じ場面で比重という言葉をよく使いますが、同じ温度域での水に対する物質の一定体積の質量の比を比重といいます。
吸水率
所定の形状の成形試験片を水中に浸漬して吸水による重量の変化を百分率で算定します。
一部のプラスチックでは、水中に浸漬している間に水に溶出する成分を含むものがあり時として体積変化を伴う場合があります。
また吸水率はその時の水の温度や浸漬時間によって違いが出る場合があり、目的の製品が温度変化や水分の影響を問題視する場合は
この点をよく検討してプラスチック成形材料を選定しなければなりません。
接着性
溶剤または接着剤を用いてプラスチック成形品の二つの面を接合して相当の引き離し力に耐える程度に密着し得ることです。
熱可塑性樹脂の中では非晶性樹脂は溶剤接着ができますが、PAを除く結晶性樹脂や熱硬化性樹脂は通常、溶剤接着は出来ません。
よって必要な場合は接着剤による接着となります。接着においては必ず適切な溶剤や接着剤を使用しなければなりません。
耐酸性、耐アルカリ性、耐溶剤性
酸、アルカリ、または溶剤によるプラスチック成形品の外観変化や特性低下などの腐食に対する抵抗性を調べるものです。
印刷や塗装などの二次加工を行う際にも抵抗性を把握しておく必要があります。
熱的性質
比熱
プラスチック成形品の単位重量に(1g)対する熱容量を比熱と称し、一般的にはこの場合のプラスチック成形品の温度を
1°だけ高めるのに必要な熱量として表され、熱伝導率と同様に製品設計の際の昇温性を検討するための目安になります。
ビカット軟化点
所定の形状、寸法のプラスチック成形試験片の中央部に1kgの荷重を有する直径1mmの先端が平坦な針を乗せ、60分あたり50°の速度で温度を上昇させ、試験片が軟化して針先が1mm進入した時の温度を表しています。
低荷重、短期間での耐熱性に対する目安となるものと考えられます。
荷重たわみ温度(熱変形温度)
高温化でのプラスチックの剛性を測定する方法として荷重たわみ温度というものがあります。
一定荷重下で一定速度で昇温を続け、試験片が所定の変形量(0.254mm)を示すときの温度として求められるもので
非結晶性樹脂では荷重たわみ温度はガラス転移温度の下限に近い温度を示すので多少実用の目安にはなります。
しかし結晶性樹脂において荷重たわみ温度はガラス転移点と結晶融点との間の温度を示すので
理論的にも実用的にもあまり意味が無いとされています。
ビカット軟化点と同じく低荷重、短期間での耐熱性の目安となります。
線膨張係数
一定の圧力のもとでプラスチック成形品の温度を1℃高めた場合に膨張する割合を表すものです。
単位長さに対する線膨張係数として表され、プラスチック成形品の温度上昇に伴う寸法変化の程度を知るために
重要とされる要素の一つです。
熱伝導率
熱伝導率は温度差が1℃で面積が1㎤、暑さ1cmのプラスチック成形品を1秒間で通過する熱量で表される。製品設計の際の目的物の断熱性を検討する際の目安となります。
脆化温度
所定形状、寸法の成形試験片の一端を試験片つかみ具でつかみ、試験そうに固定し所定の各段階の低温の伝熱媒体中に浸漬、3±0.1分置いた後、ハンマーで衝撃を加え、試験片の破壊結果から脆化温度を求めます。
これは低温下で使用の場合の設計に必要とされています。
ガラス転移点と融点
ガラス転移点(Tg)高分子物質の無定形部が過冷却されたガラス状態から軟らかい状態になる温度です。
非結晶性プラスチックではTgに達すると軟化を起こし、弾性率が低下し耐荷重性を失います。
ということは非結晶性プラスチックはTg以下の温度で使用されTgは構造体として使用可能な最高温度ということになります。
融点は一般に結晶部分の融解する温度で一次転移点とも呼ばれ成形性や耐熱性の対称となります。
ポリマーの分子構造が立体的に規則的なものは結晶化しやすく、融点をもった結晶性ポリマーとなります。
以上から非結晶ポリマーはガラス転移点(Tg)が結晶性ポリマーの場合には融点(Tm)が耐熱性の目安となります。
電気的性質
電気的性質とは
体積抵抗率、表面抵抗
所定の形状、寸法のプラスチック成形試験片に2部の電極を施し、所定の電圧を印加して試験片の表面を流れる電流を除き、内部を流れる電流を測定して体積抵抗を算出します。この際の表面を流れる電流を測定した場合には、それから表面抵抗が求められます。
体積抵抗は一般に温度上昇に伴い低下する傾向があります。また製品の使用条件や環境条件によって体積抵抗が低下する場合もあるので製品設計の際には留意しなければなりません。
誘電率
所定の形状、寸法のプラスチック成形試験片の誘電率は通常、誘電体の静電容量と空気の静電容量との比として求められますが
これは電気回路の電気容量を示す数値で高周波回路の場合の抵抗値を決める定数に相当します。
従って、この値が小さいほど高周波絶縁性が良好になります。
耐アーク性
所定の形状、寸法のプラスチック成形試験片の表面に取り付けた電極によって放電を行い、試験片が焼け焦げて絶縁性を失うまでの時間を
アーク抵抗値として測定するものです。
プラスチック成形品の表面に放電が起こった場合の放電の程度と成形品の絶縁低下との関係がわかるのでスイッチ類などの耐アーク性を必要とする製品設計において非常に大切な項目となります。
燃焼性
所定の形状、寸法のプラスチック成形試験片の一端を固定し、他端に無色炎のブンゼンバーナーで点火させ規定時間後バーナーの炎を取り去り、燃焼時間を測定して燃焼性の程度を調べます。
電気製品などを設計する場合の重要な要素となります。
成形性
成形性とは、まさに成形に関して非常に関わりの深いものです。
プラスチック成形加工の際の難易の程度を表すもので、加熱加圧下での流動性、熱安定性、成形温度および圧力範囲、冷却速度、離型性の難易度、成形収縮など様々な要素が含まれます。
再生原料を取り扱う中でもよく要望としてメルトなどの言葉がよく聞こえてきます。
メルトマスフローレイト(MFR)
一定の加熱温度と圧力によって溶融樹脂をオリフィスから押し出した時、10分間に流出する量で表し、熱可塑性プラスチックの溶融流動を示すものである。
ASTM D1238では内径2.095±0.0005mm 、長さ8.001±0.005mm のオリフィスからプラスチックの種類で異なる所定温度および所定荷重での10分間あたりの流出量(g)を求める。
また新たにプラスチックの種類で異なる所定温度および所定荷重での10分間あたりの流出量(容積)を求めるメルトボリュームレイト(MVR)が試験項目として加わっています。
一般的にプラスチックの加熱溶融時の流動性や加工性はメルトマスフローレイトの数値が大きいほど良好とされていますが
この方法は実際の成形加工の場合よりも、せん断速度が著しく小さいので、特にせん断速度による流動性の変化の顕著なプラスチックの場合や異種プラスチックに対する場合の流動性の実用的な比較にはあまり役に立たないとされています。
成形収縮率
成形収縮は成形過程における金型材料と成形品との熱膨張率の差、金型から成形品離型後の除圧による弾性回復、離型時の変形、結晶性樹脂の結晶化による体積変化などが原因となります。
成形収縮率の算出は成形金型寸法と、成形品の収縮した寸法との比で表し、金型キャビティ内での材料の流動方向でも相違する場合があります。
スパイラルフロー
熱可塑性樹脂の射出成形過程での流動性を知るための実用的な方法として、目盛付きのスパイラル状のキャビティを有する金型が採用されているそうです。選択されたプラスチック成形材料の流動性を測定し、金型設計や成形条件の設定に対する基本概念を知ることができます。
参考:化学工業日報社 成形材料商取引便覧